- Can I open two savings account in the same bank?
- Best 30 business ideas to start in Jamaica
- Business ideas or opportunities for couples
- Best Construction Apps
- What is a Postal code on a debit card?
- How to start a lip gloss business?
- How to Start a Mini Supermarket ?
- Difference between PCAOB and AICPA(PCAOB Vs AICPA)
- How to start departmental Store?
- What is Outstanding Salary?
What is the standard cost?
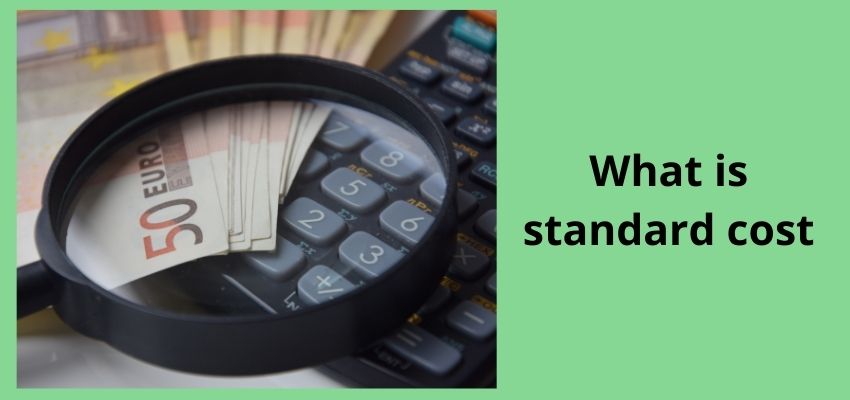
Standard cost is an assumed cost that is decided by the company before starting the production process so that they can get an idea of the product-making budget. Standard cost is not a fixed cost that cannot be said to be a real cost, it is just an expected cost. During the production part, the company tries to stop extra expenses on unnecessary things to get success with standard cost. They need to maintain their standard cost to work under a budget.
Does standard cost help to work under a budget?
Yes, of course. Standard cost is good to prepare a budget. It is a deadline for a company that they have to spend as much as they set the standard cost. Obviously, the real cost is different from standard cost but it’s a plus point by which companies can increase the selling price. Standard cost provides strength if it is higher than real production cost but if the real cost is higher than the standard cost, it is not beneficial.
What standard cost includes?
Standard cost includes direct materials, direct labor, and overhead costs, it is a combo of cost. The Cost of goods sold is calculated for product production so that they can save more of the expenses and also can be familiar with all unexpected expenses. All incurred costs whether standard or actual are recorded in the accounting books for future comparison.
Where standard cost (SC) and actual cost (AC) are recorded?
Both standard cost and actual cost are recorded in accounting books into a variance account for better comparison by the accountants for knowing the estimation of normal cost for the next years. Recorded books help to reach a final decision for improving the business strength. Due to drastic and dynamic changes in business, business suffers from unwanted expenses that’s why normal costs are calculated from the difference of actual cost and standard cost.
The decision regarding production cost is taken on the basis of the difference of actual cost and standard cost to know the expected cost for future production but it can’t depend totally on that and make their own estimation to calculate the cost. The management always finds the best techniques to improve their product cost by incurring less expenses. That’s why with the standard cost they start investing capital on expenses to complete the production cycle. The final decision is taken at the end after comparing both costs ie. actual cost and standard cost.
Why is it better to calculate?
- It is better to calculate to generate future expectations based on past events.
- The three costs estimated in standard cost help to determine the future production cost and increase the chances of better production efficiency.
- The statistical techniques are applied to find new standard costs that try to reduce more costs to produce the products on a better level.
- Also, the techniques determine the production period of actual cost with labor cost, materials, manufacturing overhead to decide the company’s future cost reasonableness.
- It is a handling tool for a producer to avoid disbalance in production activities.
- At the time of estimating the products by their cost, the standard cost is compared with the actual cost incurred in making the products.
Straight benefits of standard cost (SC)
The Actual cost cannot be determined in advance before producing the product and it is impossible to set an accurate cost for a specific product or to increase the demand for the product. In that case, companies need to move on the budgeting process, it is done with the standard cost that does not affect the actual cost.
- It is an assumed cost that is decided in the initial step, which means the company needs to stay on the estimated line to produce the products, they can’t cross that line or disbalance in terms of budget. It is a plan of saving the capital to not invest more before executing the production.
- During the production process, the management needs to focus on estimated standard costs to work accordingly. It could be safe if you follow the standard cost for the company’s financial stability.
- After completing the product production, we measure the actual cost by calculating the expenses incurred in producing the products. If the actual cost is less than the standard cost, it is a favorable variance but if the actual cost is higher than the standard cost, it is unfavorable variance. Basically, statistics tools are used to measure this comparison or differences and also help to evaluate the actual reason why AC increases than SC. According to the tool result, companies need to take action to reduce the cost as soon as possible.
- It helps to increase the value of products in terms of the selling price.
Who set a standard cost?
The management’s experience and technical experts are required to establish a standard cost which means they are only responsible for the actual cost exceeded. It is like a task that performs outside the boundary. The task is performed by total labor cost, material cost, and overhead cost which is called Standard Cost. Always keep in mind one thing, the standard cost is never equal to the actual cost, either it will be higher or it will be lower.
The company’s experts try to understand the product’s quantity and its raw materials by using their skills and experience to design a product costing that includes those three costs. When the standard cost proves the right estimated cost, a decision is taken accordingly but it keeps changing when any disturbance faces.
Read more…